Altyor’s main DNA gene: quality
Quality is at the heart of everything at Altyor
With almost 20 people in our quality department, Altyor is a certified subcontractor for major groups such as Somfy, Schneider, Valeo and Mitsubishi. Our quality organization is 360°: management system, processes and quality.
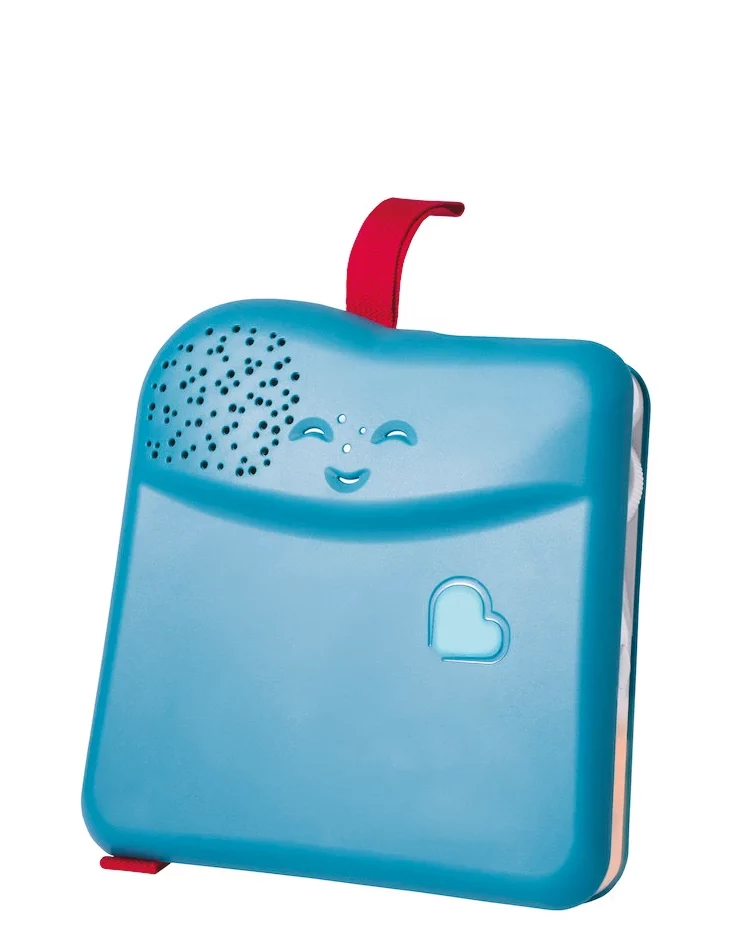
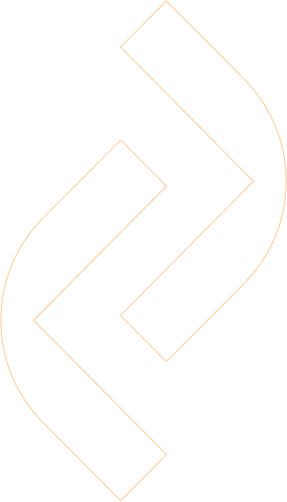
Our quality policy
Under the axis of the Mission-driven company, strategic priorities and their corresponding challenges have been established. Quantified strategic objectives have been set for these challenges.
Here are the 5 axes of Altyor’s quality policy:
01
Customer harmony
We want every customer to have a strong and rewarding experience with Altyor.
02
Fulfilment, cohesion and responsibility
We want every Altyormate to flourish in his or her mission and in the company.
03
Supply chain and purchasing efficiency
We are optimizing our supply chain management and working to improve relationships with our suppliers.
04
Profitability and financial performance monitoring
Risk, profitability and investment: Altyor strikes the right balance.
05
Process maturity
We aim to work efficiently by following optimized processes aligned with our corporate strategy.
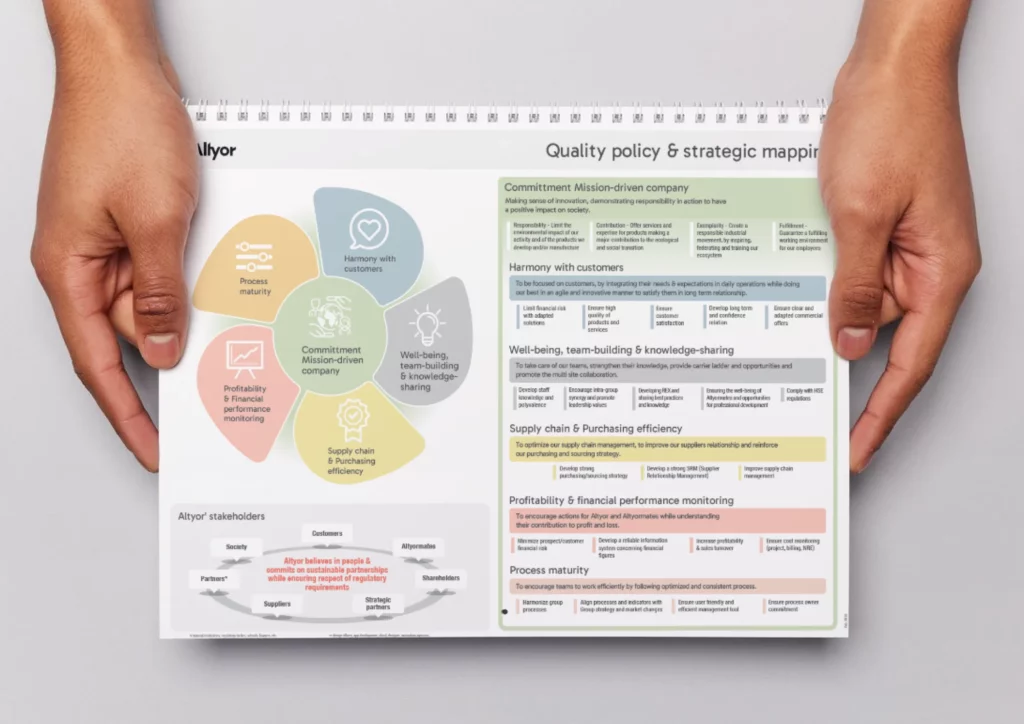
Altyor processes
Altyor’s quality management system is based on a process approach, corresponding to the operational functioning of the company, a global and transversal vision, independent of the functional structure.
3 processes are defined within Altyor:
Project management at Altyor is therefore subject to customer processes. Each milestone is validated by a customer validation and associated deliverables. We iterate through the key phases (prototyping and going into production) to ensure the project’s increasing maturity, while controlling the risks that are the subject of DFMEA and PFMEA analyses.
Our industrial processes are ISO 9001 certified and have also been audited by major groups.
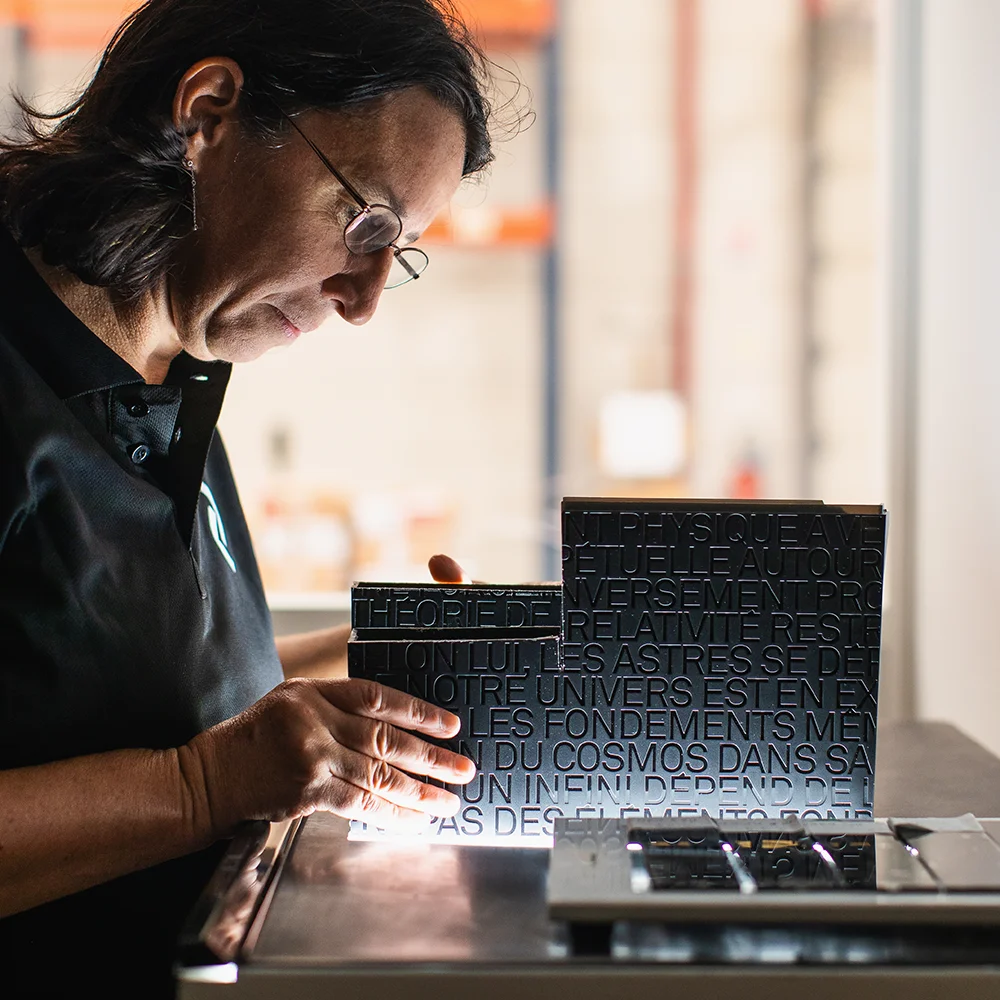
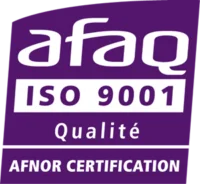
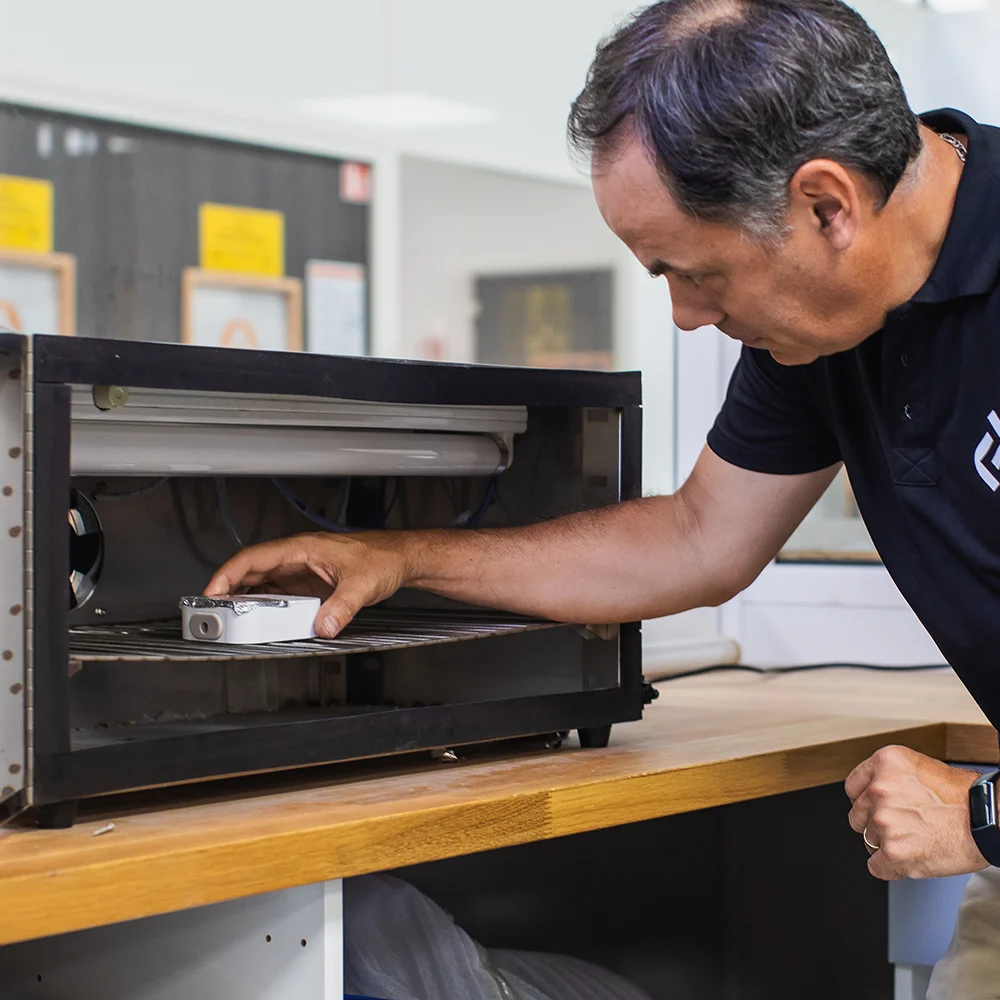
Product quality
On-line products are tested to guarantee consistent quality. In addition, each project is subject to a control plan tailored to the customer’s needs, with a quality engineer dedicated to monitoring it. The control plan consists of listing all potential problems by station and defining control frequencies to enable monitoring and a posteriori analysis of causes.
We also guarantee transparency with an open BOM, and deliveries as they come in.
With Altyor, it’s also about project and product confidentiality. The customer’s intellectual property is therefore protected.
Product quality is also closely linked to its design and industrialization.
Can we help you with your project?

How do you perform a life cycle assessment (LCA)?
We can help you calculate and analyze your product’s ecological footprint using LCA.
Life cycle assessment is the starting point for understanding your product’s impact on the environment. To help you understand the ins and outs of LCA (Life Cycle Assessment), we’ve put together 14 answers that will shed some light on the subject.