Altyor’s recycling loop
Recycle to reclaim materials from your connected product
The recycling loop, from product recovery to the injection of recycled material into a new product, via dismantling and shredding, means that today’s products are 100% composed of recycled material.

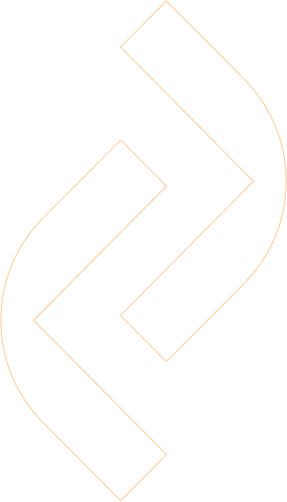
What is the purpose of the recycling loop?
Our Recycling loop has been in existence since the 2000s, and its exclusively French version since 2020. This loop has been built around French partners who are experts in recycling or injection molding. Each step in the recycling of plastic is key, with the ultimate goal of creating clean, re-injectable recycled material. Indeed, each decision can be crucial: poor sorting can result in black spots on the reinjected product, or poor homogenization can lead to loss of technical performance and color instability.
In the recycling chain managed by Altyor, a wide range of engineering plastics such as ABS and PC are processed, resulting in 100% recycled products in a wide range of colors.
What are the stages in a recycling loop?
01
Product recovery
Product recovery is obviously the first step in product recycling, but it’s also the most difficult.
Altyor offers a few business model tips to help you through this phase.
02
Dismantling
The next step is dismantling. The electronics must be separated from the mechanical components. On the electronics side, certain components containing rare metals can be recovered and recycled through specialized channels.
As for the mechanics, you need to separate the elements according to their type of material. For example, silicone must be separated from plastic. This step is also very important. The better it is done, the cleaner and more suitable the recycled material will be for re-injection. This stage also shows the advantages of eco-design upstream: eliminating bi-material products, avoiding labels stuck on plastic, banning ultrasonic welding, etc. All this experience means that Altyor can now achieve a stage 2 without complexity.
03
Shredding and removal of ferrous elements
In this stage N°3, all the plastic elements by material and color are crushed to obtain a material in the form of chips.
On leaving the shredding machine, the material is passed under magnets to remove ferrous elements.
This is its final cleaning phase. Thanks to our expertise in eco-design, implemented during product development, and careful dismantling, there will be no need to clean with water. The reground material is now ready to enter the recycling loop with a minimum of pollution.
04
Homogenization
This phase is very important. Its objective is to make the material homogeneous in terms of color, texture and behavior over a batch of several tons.
Poor homogenization can have consequences for the material’s technical and aesthetic qualities.
05
Extrusion
Extrusion or regeneration enables us to reconstitute a raw material in the same shape as a new (or virgin) material. How does it work? Recycled pellets are placed in an extruder, a machine consisting of a heated tube through which a rotating worm screw passes. At the end of this process, the material is softened, formed into spaghetti and cut into granules.
06
Injection
The recycled material is now ready to be used in an injection mold to create a new object!
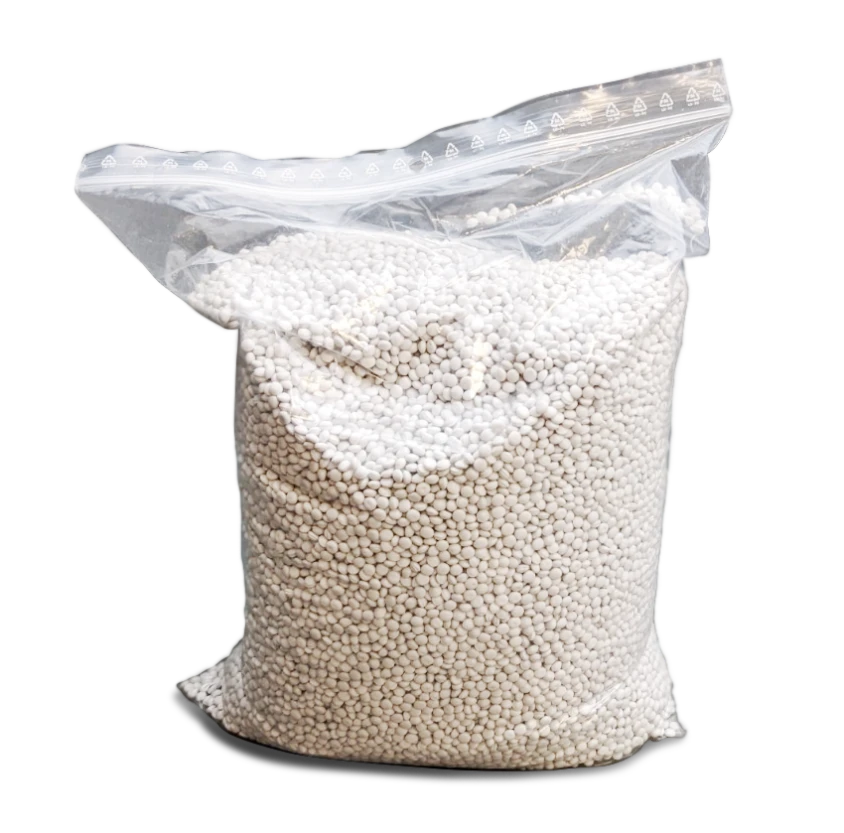
The different types of loop: open and closed
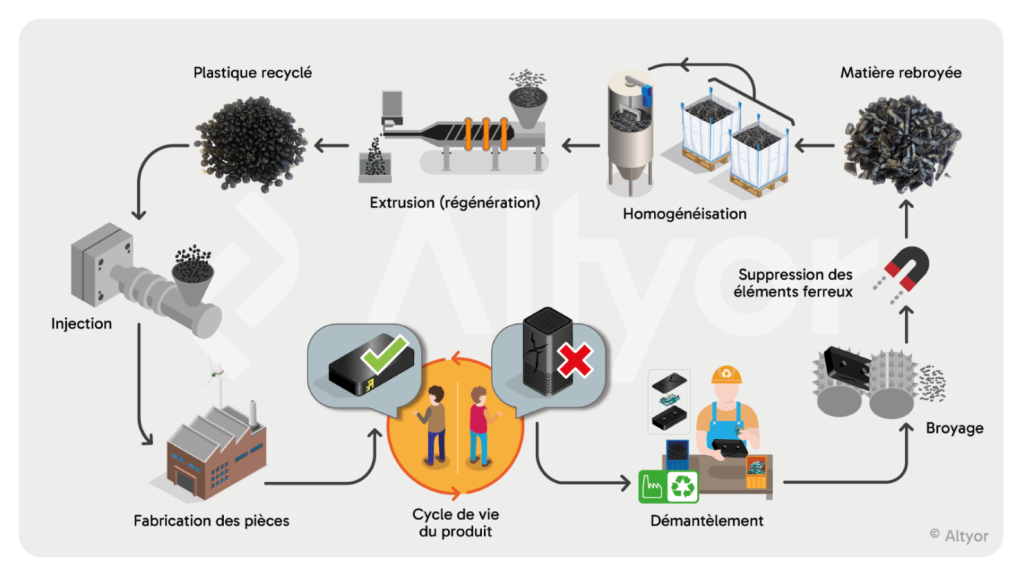
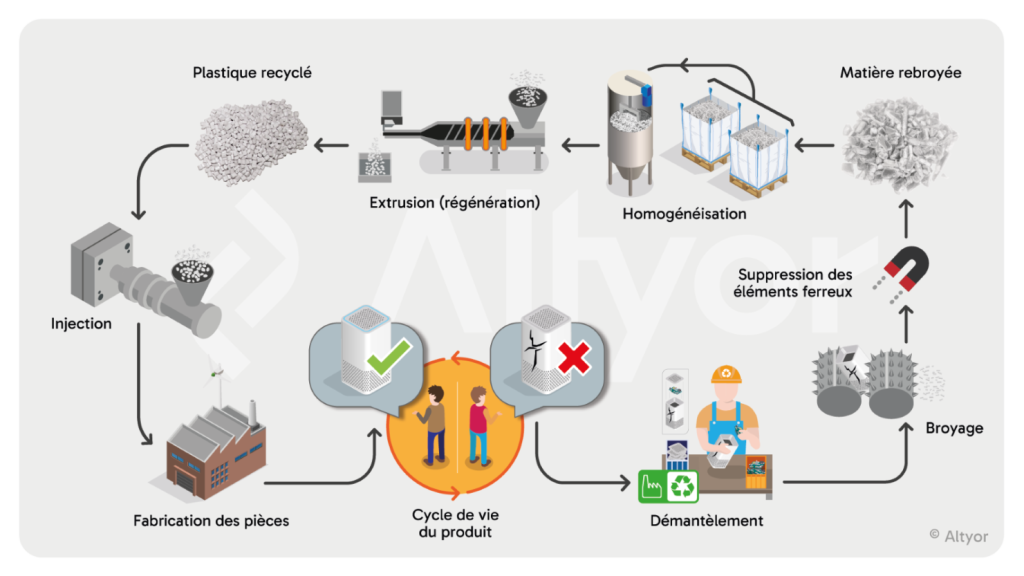
Can we help you with your project?
Why set up a recycling loop?
There are several reasons for choosing to set up a recycling loop.
First and foremost, setting up a loop is a responsible choice that positions you as a player in sustainable products. It means making the decision to use recycled plastic and controlling the end-of-life of your products. Choosing recycled material is a real lever for reducing the environmental footprint of your products, and you’ll be providing a real solution for your end customers when they no longer use their products.
The second reason is that, in the case of a closed loop, you have even greater control over the quality of the material, since it is itself derived from your products. In addition to quality, you also have control over quantity and can control your material stocks.
Lastly, the Altyor teams’ tight control over the process means that the cost of recycled material is limited, and does not exceed the purchase price of a new material.
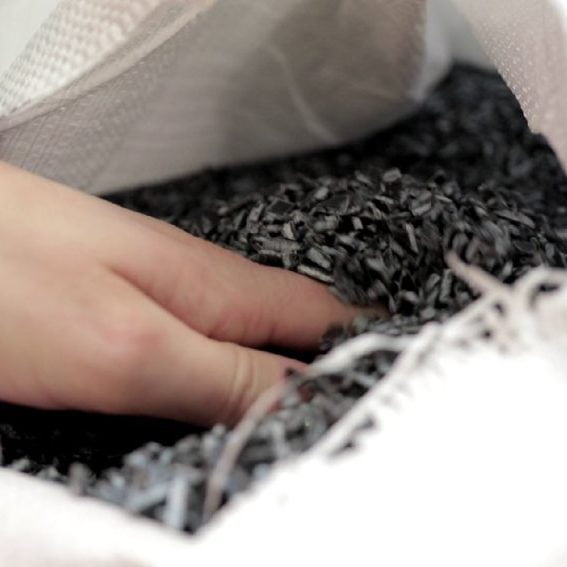
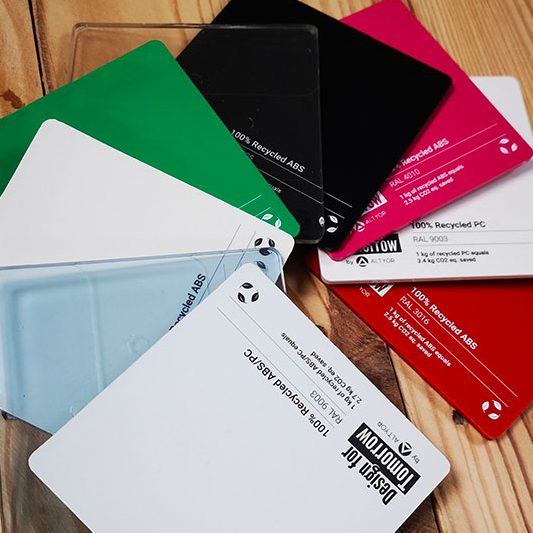
How do you set up a recycling loop?
Thanks to its expertise and network of partners, Altyor has created a recycling loop that can be adapted to each product. The Altyor loop, created with French players, is effective and enables millions of recycled plastic parts to be produced every year.
And beware of preconceived ideas about limited color choices or defects in appearance! Recycled plastic is full of surprises.