The essentials of rapid prototyping
Definition of rapid prototyping
The term “rapid prototyping” could not be clearer: the aim is to produce one or more prototypes quickly, reducing the time usually required for this kind of exercise.
Why is it worthwhile, even beneficial, to reduce these lead times? To devote the time saved to other operations, to other stages. It’s not a question of saving time to save money – as the saying goes. Nor is it a question of doing things faster but worse, of implementing a “quick and dirty” approach, as the Anglo-Saxons say. Quite the opposite, in fact. If rapid prototyping is fast, it is so that it can be repeated and reiterated to improve and refine the prototype. The aim is not to quickly get rid of this stage and move on to the next, but to ensure that the prototype is as close as possible to what the final product should be. The aim is to do things faster, but above all to do them well, to do them better. And since rapid prototyping also saves money, it’s a solution with nothing but advantages.
Technologies: 3D printing or CNC machining
Two technologies are used for rapid prototyping: 3D printing and CNC (computer numerical control) machining.
What do these two processes involve?
The aim of 3d prototyping is to add material, little by little, layer by layer: this is what we call additive manufacturing. CNC prototyping, on the other hand, aims to remove material just as meticulously from an initial block. This is known as subtractive manufacturing.
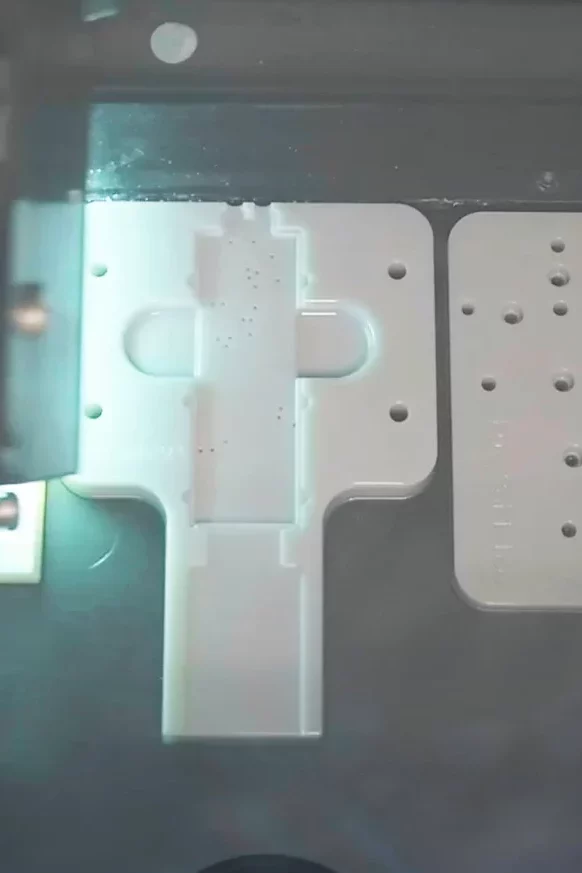
3D prototyping and CNC machining are equally effective, but often meet different needs. The former can be used to produce geometrically more complex parts, while the latter can be used to manufacture larger objects.
In environmental terms, 3D prototyping is more virtuous, since it generates no waste or loss of material.
In contrast, the very principle of CNC machining is to “waste”, to destroy previously produced material. Whichever option you choose, rapid prototyping offers greater flexibility and freedom when it comes to creating prototypes. It also allows us to be more attentive to the demands of customers or future users. This is known as design thinking prototyping.
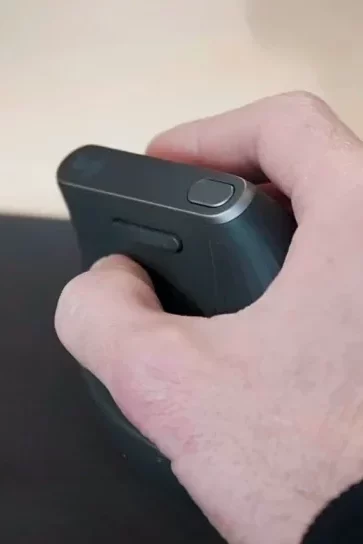
What is design thinking prototyping?
Thanks to rapid prototyping, the creation of a prototype is no longer the sole responsibility of the manufacturer: it is also the fruit of exchanges with those who will later use the final product.
This is what we call design thinking prototyping. This concept of prototyping is not limited to making a prototype according to pre-established specifications. It is more global, taking into account the demands and needs expressed by users.
In this sense, design thinking prototyping encourages listening, exchange, understanding, collaboration and experimentation. Feedback from customers and/or users enriches the process and, in turn, helps to improve the prototype. Simply because ideas are born of exchanges. It’s by taking external opinions into account that it’s possible to enrich the proposal and correct any shortcomings, validate certain choices or, on the contrary, abandon others.
In this sense, design thinking prototyping is an open, empathetic approach that relies on collective intelligence. All the more so as rapid prototyping offers a freedom that traditional prototyping lacks, thanks in particular to 3D prototyping.
The benefits: why use rapid prototyping?
There are many reasons to use rapid prototyping. Whereas it is usually necessary to make a very expensive mold to produce a single prototype (industrial prototyping), thanks to CNC machining, and even more so thanks to 3D prototyping, it is possible to design and manufacture several, without first making a mold. This method enables us to improve the product to get as close as possible to the one that will be industrialized.
This is known as functional prototyping. The first step is to understand user needs and define precisely what the product should deliver. Once this phase has been completed, an initial, rough prototype is drawn up, bringing together the main functionalities. This prototype is subjected to tests that highlight potential problems, modifications to be made and necessary improvements. During functional prototyping, the prototype is refined and perfected. It is then possible to enhance it, modify its design, try out a new material. The material can also be tested for appearance, strength, feel, etc.
This process is all the more important as it enables us to gather users’ opinions and comments, and thus respond directly to their requests and needs. Functional prototyping is a kind of continuous improvement process, with the ultimate goal of producing the “ultimate prototype”. It avoids the pitfalls encountered when a product is launched on the market without this prior process.
Functional prototyping is all the more useful as an elaborate prototype, close to the final product, can also help convince potential commercial partners, whether distributors or investors. And all this at low cost, since a prototype can be developed by simply modifying a 3D computer file.
How do I create 3D rapid prototypes?
Indeed, the first phase of 3D prototyping is purely digital. To carry out this virtual work, 3D modeling software is essential. Without this tool, it’s simply impossible to design a prototype.
In fact, it’s this software that first enables you to draw and design the prototype. But that’s not all: it’s also what enables you to modify the initial 3D file to make the necessary changes to the first prototype. Without modeling software, 3D prototyping and functional prototyping are impossible. All the more so as it is this software that drives the 3D printer, in the same way that office or layout software drives printing on a traditional printer.
The second essential link in the 3D rapid prototyping chain is the 3D printer. It’s the printer that takes you from idea to product, in this case to prototype. Once these two components are combined, it’s possible to move from the virtual to the concrete. To do this, it is essential to have a wide range of skills, covering consulting, development and product industrialization. This means taking charge of complete project management, following customer specifications and carrying out functional prototyping, in order to validate the choices made during the design phase and implement them during development. 3D prototyping enables us to select the manufacturing processes, materials and techniques that will provide the final product with the required functionality.
What are the stages in the 3D prototype manufacturing process?
Whatever the type of 3D printing used, or the size and complexity of the prototype to be produced, the process always begins with 3D modeling. This can take varying amounts of time, depending on the complexity of the project.
Once this stage has been completed, it’s time to prepare for printing, checking the parameters and quality of the digital file. If everything is in order, this 3D file is sent to the printer, which will then materialize it. To do this, the printer proceeds layer by layer, using different materials. These are often thermoplastic filaments (FDM process, for fused deposition modeling), such as ABS, PLA or nylon. These filaments sometimes incorporate other components such as ceramics, wood and polymers.
Stereolithography (SLA) and digital light processing (DLP) use resins. Selective laser sintering (SLS), direct metal laser sintering (DMLS) and selective laser melting (SLM ) are powder-melting technologies used to manufacture prototypes in polymers or metals such as aluminum, stainless steel or titanium.
Other machines specialize in printing organic materials such as wax, foodstuffs (pasta, chocolate, etc.) or even human cells and tissue. Once these prototypes have become reality, they need to be finished – especially those in metal – so that their appearance is flawless, just like that of industrialized objects.
Can we help you with your project?
IoT expert, from eco-design to industrial production of connected objects
We are a major player in the field of the Internet of Things (IoT). Our raison d’être is to provide complete solutions, from IoT strategy to the design and manufacture of connected objects, all from an eco-responsible perspective. With almost 30 years’ industrial experience, we benefit from multidisciplinary expertise and passionate, committed employees.
Within our company, we have mechanical and electronic design offices, and an integrated production capacity that enables us to turn our customers’ ambitions into reality. More than 250 companies worldwide have already chosen Altyor to industrialize their products, including nearly 140 connected concepts that have found their place on the market. The diversity of our customers’ business sectors and the variety of their structures testify to the flexibility, high quality standards and culture of innovation that characterize our company. We are also actively committed to the ecological transition, emphasizing our expertise in eco-design, a thoughtful approach to manufacturing and the promotion of circular economy channels.
From design to industrialization, production and remanufacturing, we offer ongoing, customized global support to ensure the success of your project.
01
Innovation support
_Building a solid foundation for your industrial project
02
Mechanical and electronic design
_Giving lasting life to your product
03
Industrialization
_Industrializing your product to make your production more reliable
04
Production
_Implementing your robust production line
05
Remanufacturing
_Supporting your product’s life cycle