Nicolas Garcin, ingénieur électronique chez ALTYOR, nous donne son TOP 8 des conseils pour comprendre l’importance des bancs de test, passage obligé dans l’industrialisation d’un produit électronique.
#1 – A stage not to be missed
A test bench is a piece of equipment used to check products as they leave the production line, to ensure that they comply with specifications. These tests could be carried out manually, but automation makes them safer and more standardized.
In production at ALTYOR, 100% of electronic boards are tested. A PCBA (Printed Circuit Board Assembly) can behave differently depending on the components and battery it contains. Tests are therefore carried out to ensure uniformity and guarantee that your products sold will be faultless.
#2 – Two test benches for maximum reliability
There are 2 types of test bench for testing electronics:
- Pre-assembly test benches to test the electronic board, in particular the sensors positioned on it before final assembly.
- Test benches assembled to test the electronic functions of the finished product
#3 – Software-Firmware et mécanique
The test bench consists of two components:
- Software: developed specifically for the product, this software is responsible for chaining together test scenarios linked to the firmware and electronic board, controlled by the test bench.
- A bed of nails (mechanical part): also specific to each product, these consist of a number of metal pins which touch the contact points on the electronic board.
#4 – Be careful with test points: put them in the right place!
PCBA contact points are used to control key functions. Their positioning must be considered at the design stage.
In the case of an already assembled product, tests can be carried out using contact points under the battery door (if you have one and if your design allows).
For smaller products, without the space required for contact points, testing is carried out by wireless link (Bluetooth, Wi-Fi…). However, the voltage test will necessarily require a wired contact.
Having test points, even better if they are accessible without opening the product, makes it easier to carry out diagnostics in the event of reworking or product return. So beware of removing them!
#5 – Think about the legal aspects
The benches generate labels with legal traceability information: CE, RoHs, serial number, manufacturer’s logo and address. Thanks to this traceability system, we can know the day a product was assembled and the day it was tested, in which box it was placed, and the date and address of shipment.
#6 – Specifications written as soon as possible
Test bench specifications must be drawn up as early as the product design and electronics phases. Don’t worry, our design engineers write them. In fact, they are used to assess what information needs to be tested, in agreement with the customer. These specifications must be consistent with the firmware, which may require several round-trips with the customer and the development of dedicated test software.
Complete and definitive validation of the test bench is then carried out on a minimum of twenty products.
#7 – Vive la communication!
Setting up communication between the bench and the product can be tedious. Particularly when ALTYOR is not the one developing the product firmware.
This firmware must communicate with our test software. So there are often many adjustments to be made, and customer-partner iterations, hence our support work.
#8 – Significant costs and delays
Le coût d’un banc de test dépend de sa complexité. On sait, en revanche, qu’en moyenne le développement d’un banc de test prend entre 6 et 8 semaines avec les interactions clientes comprises. C’est un délai important mais compressible selon le nombre des parties prenantes et leurs connaissances. Retrouvez d’autres conseils sur l’industrialisation de votre smart device
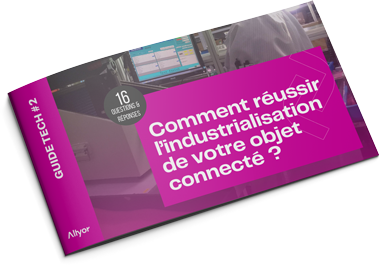
How to successfully industrialize your connected object?
Industrialization is a key stage in the development and production of an electronic product. In this guide, our experts have put together 16 key points to help you understand what’s at stake in this phase.
Test bench FAQs
Can we help you with your project?
From design to industrialization, production and remanufacturing, we offer ongoing, customized global support to ensure the success of your project.
01
Innovation support
_Building a solid foundation for your industrial project
02
Mechanical and electronic design
_Giving lasting life to your product
03
Industrialization
_Industrializing your product to make your production more reliable
04
Production
_Implementing your robust production line
05
Remanufacturing
_Supporting your product’s life cycle