What is Industry 4.0?
Industry 4.0, or the factory of the future, corresponds to the most recent evolution in manufacturing techniques. Factory 4.0 is driven by the introduction of manufacturing methods that exploit augmented reality, connected objects, 3D printing, robots, etc. The notions of cloud and big data take on their full meaning in the factory of the future, which assigns a predominant place to artificial intelligence. It’s a factory that works by connecting real objects to digital technology and people. Its vocation is to enable product customization. Indeed, new technologies provide the tools to meet the expectations of consumers who are looking for unique products that are still affordable.
The fourth industrial revolution is making it possible to optimize process flexibility and increase reliability, while maintaining high production capacity. Digital advances also make it possible to keep production costs under control, despite the small number of items machined and marketed in response to customization needs.
Industry 4.0 is therefore defined as a vector for reducing energy consumption and labor-related expenses to give rise to qualitative, unique and less expensive products.
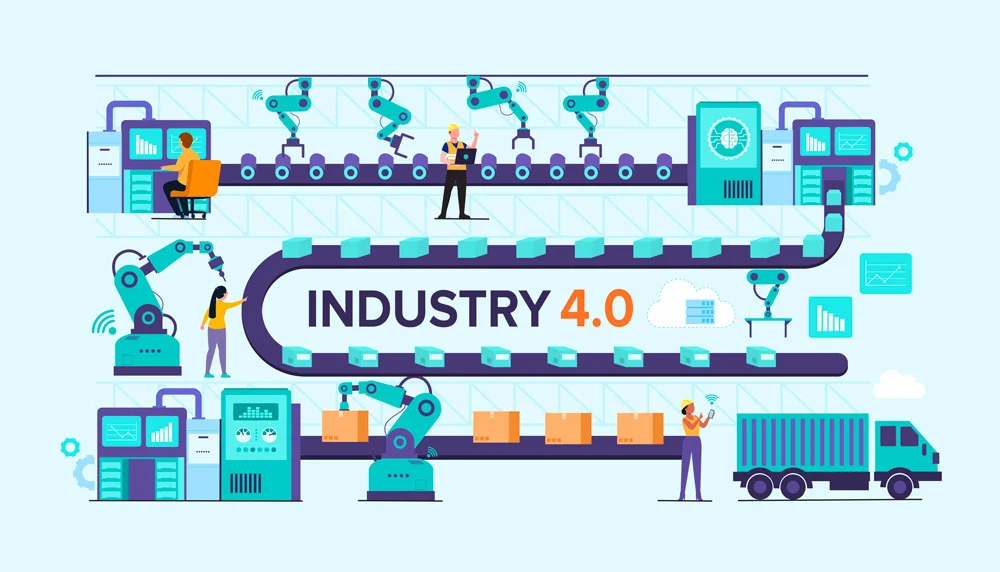
Where does the name “Industry 4.0” come from?
Driven by technological advances, a new industrial revolution is taking place. We’re talking about Industry 4.0, which is unquestionably oriented towards the future. But what exactly is it all about? Here are the essential facts about this new industry.
A look back at the birth of the industry of the future
1st industrial revolution
Industry 1.0 was born in 1765, driven by the boom in mechanical production. This was the first industrial revolution. When James Watt developed the first steam engine in 1769, it became easier to exploit coal to run factories. Machines gradually replaced handicrafts, increasing the speed of production. From then on, objects began to be manufactured in small series.
2nd industrial revolution
The second industrial revolution, corresponding to the birth of Industry 2.0, dates back to 1870. By the end of the 19th century, oil and electricity were being exploited to a greater extent. Manufacturing processes automatically became more modern, boosting design speeds. The chemical and automotive industries replaced steam engines with electrical equipment. Taylorism begins to be applied, making it profitable to recruit unskilled workers. The new energies harnessed by Industry 2.0 make it possible to launch mass production, i.e. the mass production of several identical products.
3rd industrial revolution
The middle of the 20th century was marked by the third industrial revolution, propelled by automation and globalization. More precisely, it was from 1969 onwards that the major changes took place. The advent of information technology and the development of electronics, not to mention the reduction in telecommunications costs, have changed the way factories operate. More concretely, workers were relieved of arduous, repetitive tasks thanks to the adoption of automation systems. Robotics was born at the same time as Industry 3.0, which favors mass production.
Some observers place the emergence of Industry 3.0 at the beginning of the 21st century. According to their analysis, it is the ecological transition that is driving these changes. The exploitation of renewable energies and the development of digital technology in resolutely innovative forms would then be the defining elements of this third revolution, driven by the exploitation of clean energies.
4th industrial revolution:
Industry 4.0 has been developing since 2011 thanks to digitalization. The term was coined at the Hannover Fair in Germany. The new revolution involves harnessing digital technologies to offer personalized products/services to consumers, without necessarily committing substantial investments. Industry or factory 4.0 lies at the crossroads of real and digital objects. It’s a connected industry that exploits the various aspects of artificial intelligence, virtual reality and everything that digital technology makes available to companies looking to boost their performance. A number of digital systems are interconnected to improve production speed, process reliability and team safety. The strategies adopted automatically enable industries to participate in the ecological transition while putting consumers at the center of their concerns.
Industry 4.0 is therefore one that is gradually sweeping away the boundaries between the physical and the digital with a view to evolving the manufacturing system.
The components of the industry 4.0
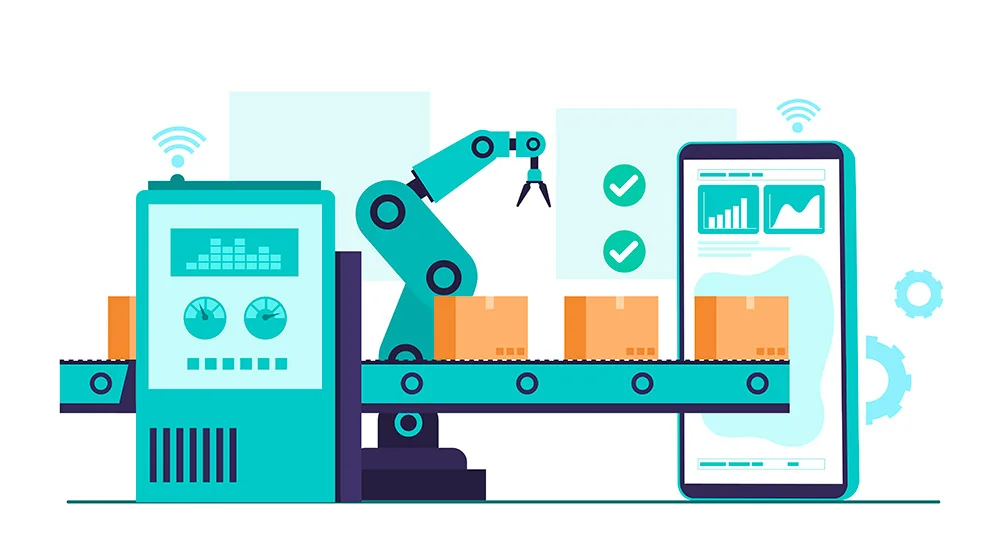
Popularized by the media, Industry 4.0 is a concept that aims to increase the productivity of companies that integrate it into their operations. This industry of the future places itself at the heart of production, enabling significant improvements to be made.
Digitization
Industry 4.0 incorporates the use of several technologies such as the Internet of Things (IoT), 3D printing, augmented reality, cloud computing, big data analytics and artificial intelligence. Factories 4.0 are equipped with state-of-the-art sensors, software and robotics. Their function is to collect and analyze data, so that the most logistically relevant decisions can be made. It is also possible to link production data with inventory, ERP and support center data. In this way, valuable information which, in previous systems, remained compartmentalized, can be made visible.
Automation
With the digitization of businesses, we’re seeing the development of automation, predictive maintenance and improved operational processes. What’s more, performance and customer experience have reached levels never before imagined.
In the smart factory, integrated sensors play a key role, providing extensive transparency of production assets. Their effectiveness in anticipating machine breakdowns ensures continuity in production.
The intelligent factory
IoT, cyber-physical systems, cloud computing and big data analytics are the main technologies on which Industry 4.0 is based. By combining these technologies, we obtain the connected factory, whose objective is to enable objects to communicate with each other and benefit from a certain degree of autonomy. Control in manufacturing is carried out via AI-based visual information, rather than manually. This is known as augmented reality.
3D printing is used to manufacture customized products based on customer instructions. The result is improved production and quality. The risk of error is reduced. What’s more, waste generation is also reduced.
Connected customer
Manufacturers can plan to equip the products they sell to their customers with intelligent sensors. This makes it possible to monitor them, particularly with regard to maintenance or malfunctions. The customer is then immediately alerted and able to remedy any problems.
In addition, to keep in touch with customers or suppliers, we may consider setting up an extranet or EDI (Electronic Data Interchange) system.
Applications for Industry 4.0
As an industry professional or someone facing industrial issues, you’re probably thinking about digitizing certain practices, or moving your business into the digital world.
This new approach provides companies with numerous tools for optimizing production lines. To better understand the benefits of moving to Industry 4.0, particularly in terms of cost and complexity, here are a few recurring examples of applications.
Save paper and consumables
The digitization of content enables companies to optimize document management in the long term: by switching from analog to digital formats, every employee contributes to reducing the time spent on redundant tasks. Errors, often caused by out-of-date data, are considerably reduced. Digitizing the business is therefore a matter of survival for structures wishing to remain competitive.
Process optimization, IoT and real-time control
Digitization is very often accompanied by the introduction of control or advanced analysis software, enabling production to be improved. At the same time, machines and equipment can be fitted with wireless sensors, enabling precise production monitoring and real-time data collection. This is the mingling principle of the IoT (or Internet of Things), enabling high connectivity.
Experimenting with 3D printing
Digitization enables us to introduce new machines into our processes, and therefore new methods for designing ever more specific and highly customized products. This is the case, for example, with 3D printers, which can rapidly produce prototypes and manufacture complex shapes to customer specifications at all times.
Extended product connectivity to the Internet
Thanks to digitalization, every factory-designed product can be fitted with sensors to monitor use, carry out maintenance and report any problems. Customers are thus alerted in real time in the event of a malfunction. Depending on usage, “intelligent” products can also incorporate services to enhance the original model.
Computer network integration
New digitization technologies make business-to-business commerce possible. Using an extranet or electronic data interchange (EDI) system, companies can stay in touch with their customers, suppliers and partners. A transactional website can also be deployed for consumer products.
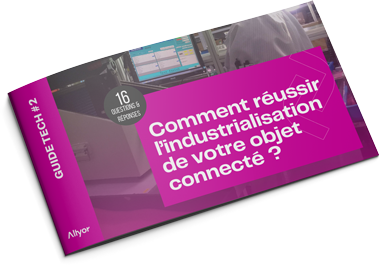
How to successfully industrialize your connected object?
Industrialization is a key stage in the development and production of an electronic product. In this guide, our experts have put together 16 key points to help you understand what’s at stake in this phase.
From design to industrialization, production and remanufacturing, we offer ongoing, customized global support to ensure the success of your project.
01
Innovation support
_Building a solid foundation for your industrial project
02
Mechanical and electronic design
_Giving lasting life to your product
03
Industrialization
_Industrializing your product to make your production more reliable
04
Production
_Implementing your robust production line
05
Remanufacturing
_Supporting your product’s life cycle